
Gravity Rollers, also known as non-powered rollers, can come in various shapes and sizes, depending on the specific application they are being used for. Gravity rollers are often found in industries such as manufacturing, distribution, and warehousing where large volumes of products need to be moved efficiently.
GCS can manufacture rollers to your specifications, applying our years of experience in materials and design for both OEM and MRO applications. We can provide you with a solution to your unique application.
Optimize Your Conveyor System
Partner with GCS in China for reliable, efficient gravity rollers tailored to your operational needs.
Key Specification
Gravity rollers specifications vary based on application needs and material handling requirements. Typical specifications include drum diameter, length, and weight-carrying capacity. Common sizes in diameter are 1 inch (2.54 cm), 1.5 inch (3.81 cm), and 2 inches (5.08 cm). The length can be determined on a case-by-case basis, generally between 1 foot (30.48 cm) and 10 feet (304.8 cm). Weight-carrying capacity typically ranges from 50 lbs (22.68 kg) to 200 lbs (90.72 kg).
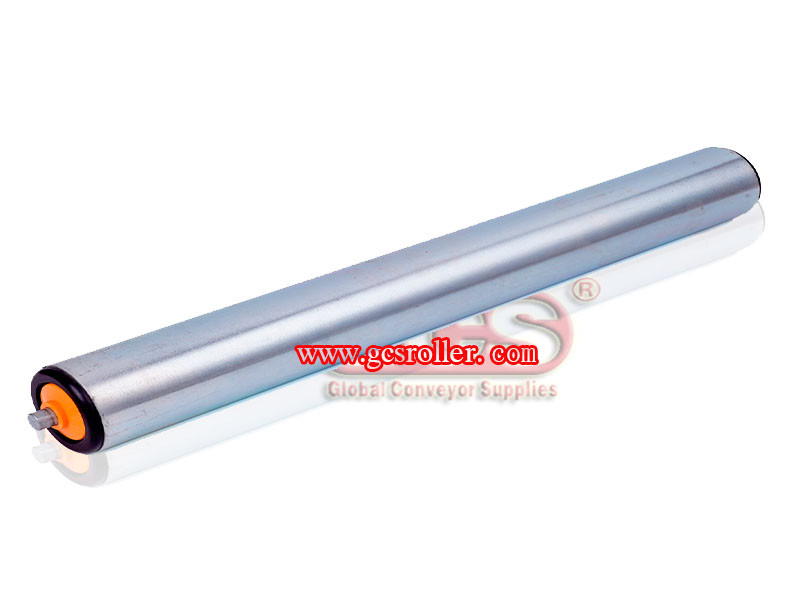
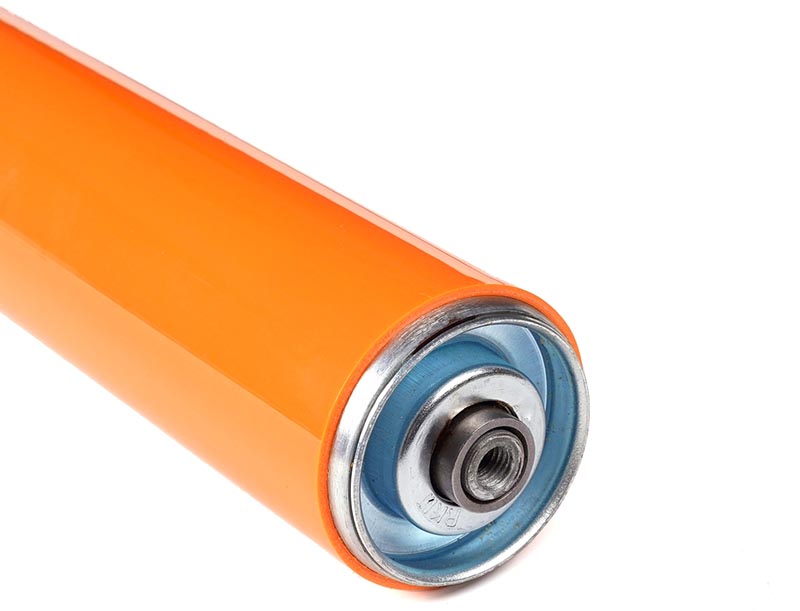
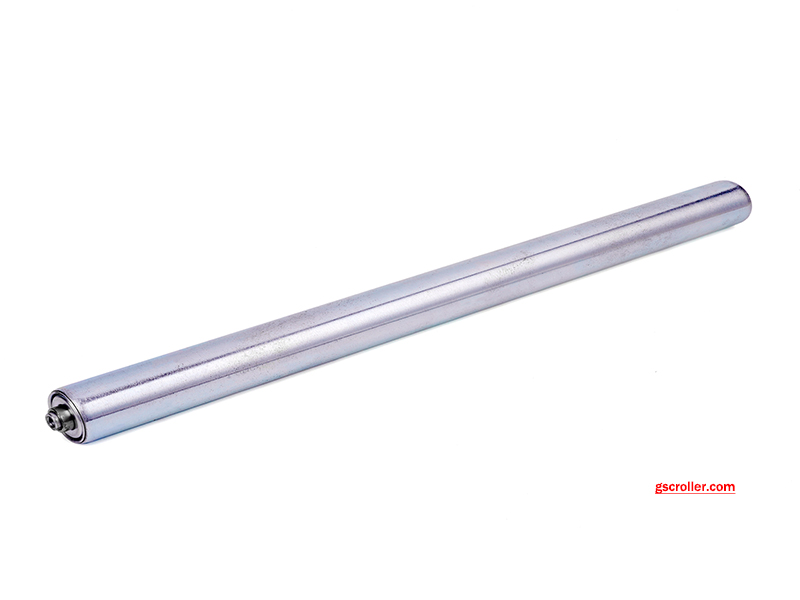
Model
|
Tube Diameter
D (mm)
|
Tube Thickness
T (mm)
|
Roller Length
RL (mm)
|
Shaft Diameter
d (mm)
|
Tube Material
|
Surface
|
PH28
|
φ 28
|
T=2.75
|
100-2000
|
φ 12
|
Carbon Steel
Stainless Steel |
|
PH38
|
φ 38
|
T=1.2, 1.5
|
100-2000
|
φ 12, φ 15
|
||
PH42
|
φ 42
|
T=2.0
|
100-2000
|
φ 12
|
||
PH48
|
φ 48
|
T=2.75
|
100-2000
|
φ 12
|
||
PH50
|
φ 50
|
T=1.2, 1.5
|
100-2000
|
φ 12, φ 15
|
||
PH57
|
φ 57
|
T= 1.2, 1.5 2.0
|
100-2000
|
φ 12, φ 15
|
||
PH60
|
φ 60
|
T= 1.5, 2.0
|
100-2000
|
φ 12, φ 15
|
||
PH63.5
|
φ 63.5
|
T= 3.0
|
100-2000
|
φ 15.8
|
||
PH76
|
φ 76
|
T=1.5, 2.0, 3.0
|
100-2000
|
φ 12, φ 15, φ 20
|
||
PH89
|
φ 89
|
T=2.0, 3.0
|
100-2000
|
φ 20
|
Application Examples Of Gravity Rollers
90°/180 ° bending gravity rollers conveyors, our conical roller conveyors powered without diagonal and diagonal angles are designed for use at 45 degrees and 90 degrees
Gravity rollers diameter, 50mm (small end). Roller material, galvanized steel/stainless steel/rubber/plastic. Rotation Angle, 90 °, 60°, 45°.
Flexible roller conveyor systems Retractable conveyors are Customised in various widths lengths and frames. Roller flexible conveyors are designed to transport goods efficiently and are economical.
The roller flexible conveyor is highly adaptable and can be pulled in and out, as well as bent around corners and obstacles, allowing for unlimited configurations. The conveyor has proven to significantly reduce the time required to transport products smoothly and efficiently, while reducing manual handling.
Spindle Conditions for Conveyor Rollers
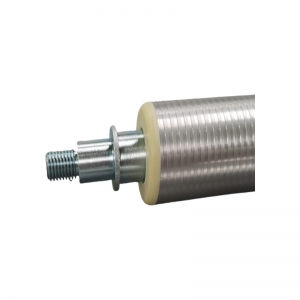
Threaded
Round spindles can be threaded at either end to suit a metric or imperial nut. In most cases, the spindle is supplied loose.
Drilled and Tapped
Round spindles with 2 milled flats are used in conveyors with slotted side frames where rollers are lowered into position. In most cases, the spindle is supplied fixed within the roller.
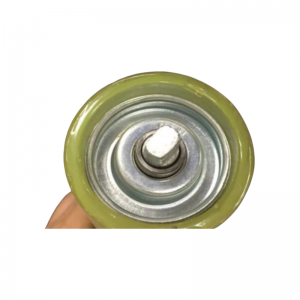
Drilled Spindle End
Round spindles can be threaded at either end to suit a metric or imperial nut. In most cases, the spindle is supplied loose.
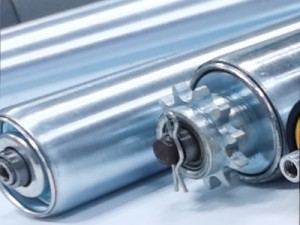
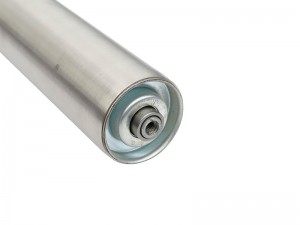
Drilled and Tapped
Both round and hexagonal spindles can be drilled and tapped at each end to enable the roller to be bolted between the conveyor side frames, thus increasing the rigidity of the conveyor.
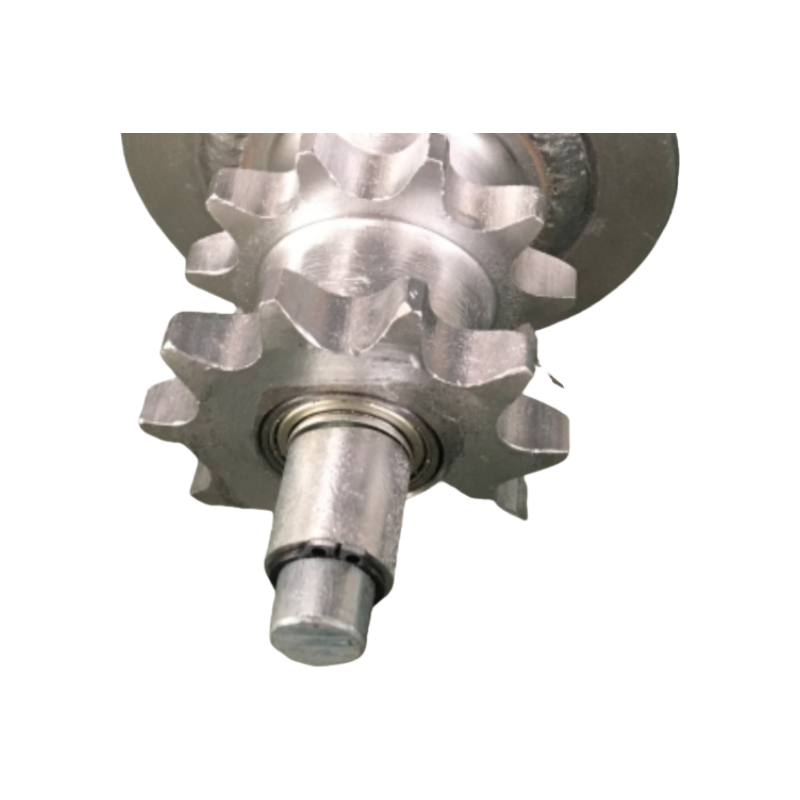
Circlipped
External circlips can be used to captivate a spindle within a roller. This method of retention is usually found on heavy-duty rollers and drums.
Hexagonal
Extruded hexagonal spindles are suitable for punched conveyor side frames. In most cases, the spindle would be spring-loaded. The hexagonal shape prevents the spindle from rotating in the side frame.
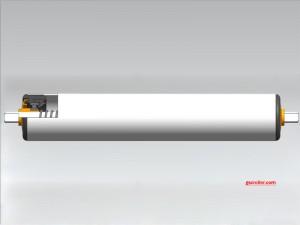
Versatile, Customized Conveyor Systems that Last
GCS presents the most versatile conveyor system rollers to suit any application. Constructed using the highest quality gravity roller conveyor systems workmanship and designed to stand even the most rigorous use, our rollers provide function and utility that you can trust.
A Wide Range of Materials
Is corrosion an issue with your processing or manufacturing business? You should consider our plastic gravity roller, polyurethane conveyor rollers, or one of our other non-corrosive options. If so, consider our PVC conveyor rollers, plastic gravity rollers, nylon gravity rollers, or stainless gravity rollers.
We also have the custom heavy-duty roller conveyor system that you need. Conveyor Systems conveyor roller manufacturers can give you heavy-duty conveyor rollers, steel conveyor rollers and durable industrial rollers.
Increased Workflow Capacity
A busy warehouse facility requires robust solutions for maximum productivity. While labor costs and shipping times may be blowing out your budget, installing our high-quality conveyor roller can dramatically increase your workflow capacity. By speeding up the processes that you use to deliver your goods by using high-quality conveyor system rollers, you will see benefits in many aspects of your facility. From a reduced burden on your employees to meet demands, as well as a safer and more efficient workplace environment, you will see a higher level of customer satisfaction and most importantly, an increase in your bottom line.
Improved Safety Measures for Any Warehouse or Facility
GCS is committed to providing the most safe and reliable rollers to suit any system or process in a busy working facility, whether the conveyor uses a gravity or powered mechanism of action. A strong and long lasting effect is produced through self-lubrication offered on many of our rollers. Suitable for a range of applications including food handling, chemical transport, volatile material movement and high capacity warehousing, our range of custom conveyor system rollers are backed by our service guarantee that ensures safe and efficient use in a consistent and durable manner.
Cost Effective Approach to Time Management
Implementing a robust conveyor roller solution to your facility need not be the expensive effort that it once was. GCS offers the most extensive range of custom conveyor rollers designed to reduce your overheads while saving you time. By automating your in-facility transportation processes with stronger and longer lasting rollers, the initial investmentinn implementing your conveyor roller will save you money on labor costs. With a focus on durability and use within a wide range of applications, our rollers far outperform more expensive products.
GCS Gravity Rollers
Finding the perfect gravity rollers for your operation is crucial, and you want to do so with little disruption to your workflow. If you need a special-size gravity roller for your conveyor system or have questions about the rollers’ differences, we are ready to help you. Our customer service team can help you get the right part for your existing conveyor system.
Whether installing a new system or needing a single replacement parts, finding suitable gravity rollers can improve your workflow and increase your system’s life. We will help you get the right part with fast communication and personalized care. To learn more about our rollers and custom solutions, contact us online to speak with a specialist or request a quote for your roller needs.
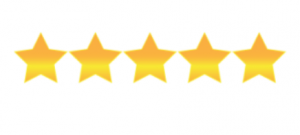